It is no secret that recalls in the automotive industry are becoming more frequent and expensive. This data from the Society of Automotive Analysts (SAA) suggests recalls are on the rise for a number of factors including a larger number of product launches and platform changes. That is why 2014 has seen a record number of vehicles recalled.
In short, and this is backed up by the SAA:
- Different models are based on the same platform, and the same parts are installed in different models à in case of a problem the impact affects more cars.
- The periods between the different model series reduced from series to series, so the time to identify and address quality issues decreases.
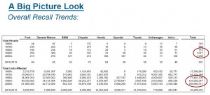
SAA data points towards an upwards trend in recalls due in part to more cross-platform parts and sub-components.
So what do automobile manufacturers and their suppliers need to do in order to handle the logistical challenges these recalls present? Beside traceability, as IFS’s Jakob Bjorklund points out in this recent podcast, quality management and quality assurance are key. Because we recognize this, we have developed extensive functionality to prevent and manage recalls.
Quality Management: Total quality management can be described as an organization-wide approach to understanding what customers need and consistently delivering satisfactory solutions within budget, on time and in keeping with corporate policies on social responsibility and environmental considerations. It’s an essential part of your day-to-day operations. The level of quality you provide has a direct effect on your revenue and expenses, it determines how competitive you can be—and it can have an enormous effect on the value of your brand.
Quality Assurance: IFS Quality Assurance provides those responsible for quality management with all the capabilities to support the requirements of the international marketplace. The solution enables users to plan compliance, schedule and execute audits, report non-conformance and record any corrective and preventive actions.
Bar Code Scanning: Our IFS Touch Apps offering includes a downloadable app that allows for data capture for seamless traceability. Automated data capture of course generates a tremendous amount of data, and
A consistent, unified data architecture across the application suite. One challenge GM in particular has faced was the lack of a master data strategy. The best quality management and assurance functionality in the world will be less effective if it has to draw data from multiple applications used across the enterprise, or at the very least a successful implementation will be difficult if not unlikely. A single unified application that spans the entire product life-cycle eliminates complexity and is probably the ideal solution for a middle market company in the automotive space.
That is why more and more automotive suppliers are selecting IFS Applications … but that can be the topic of another post on IFS’ growing footprint in the industry.